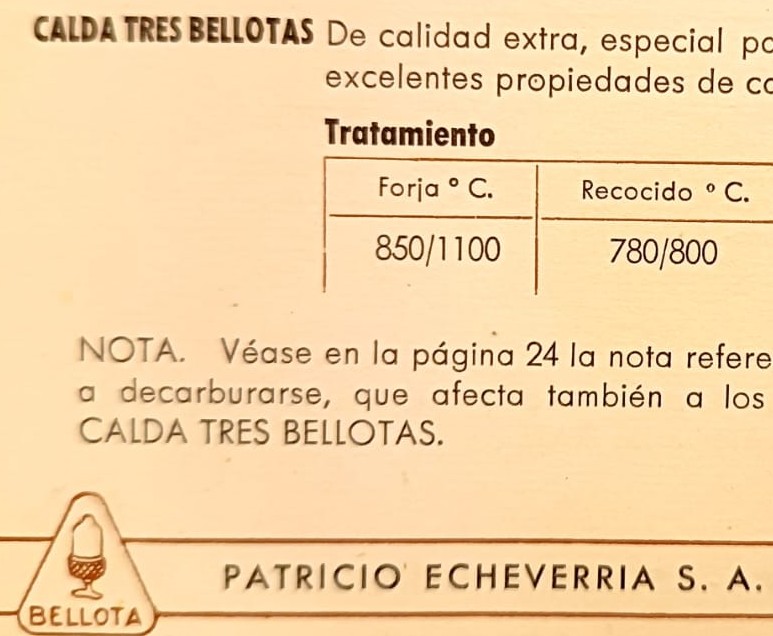
ACERO 3 BELLOTAS. ¡NUEVO!
BLOG PREMIUM DEL LABORATORIO DE FORJA
ACERO 3 BELLOTAS
Un sello que hablaba sin palabras
Durante mucho tiempo, ver el símbolo de las Tres Bellotas era un símbolo de confianza para los que compraban una herramienta de verdad. No siempre estaba grabado en el acero, de hecho, no creo que se grabara en en machetes, azadas o hoces, pero podía encontrarse en etiquetas, mangos de madera o incluso en el embalaje. Aun así, su presencia decía mucho más de lo que parecía. No era solo una marca comercial: era sinónimo de confianza, y de un acero bien hecho.
Y para muchos herreros, durante años fue un símbolo de garantía.
Por que sí, el acero Tres Bellotas se vendía.
Era un acero perfecto para calzar herramientas. Soldar un filo de Tres Bellotas sobre un cuerpo de hierro dulce era muy habitual en las fraguas.
Bellota y su acería
En 1931, Bellota instaló su propia acería en Legazpi (Guipúzcoa), basada en un horno de arco eléctrico. Este fue un cambio muy importante. En lugar de comprar acero como hacían otros, lo fabricaban desde cero. Elegían la chatarra, la fundían, la afinaban y la convertían en muy buenas herramientas.
La materia prima podía ser chatarra de alta calidad, hierro de primera fusión, obtenido directamente del mineral de hierro en altos hornos, o incluso arrabio, un hierro fundido con alto contenido en carbono. Todo esto se fundía en el horno eléctrico, que permitía un control muy fino sobre la energía y la composición química.
Durante la fusión, se eliminaban impurezas como azufre y fósforo, y se realizaban análisis periódicos del baño metálico con cucharillas de ensayo. En aquella época no se disponía de espectrometría moderna ni de análisis por combustión como los conocemos hoy. Lo que se hacía era extraer pequeñas muestras del baño y analizarlas en laboratorio mediante métodos clásicos de química analítica: volumetría, gravimetría o combustión controlada, midiendo los gases liberados para conocer el contenido de carbono. Estos análisis eran más lentos, pero permitían afinar de forma bastante precisa la composición del acero. Según el resultado, se corregía la carga: se añadían materiales carburantes como grafito si hacía falta subir el carbono, o se oxigenaba el baño si había que reducirlo.
Durante la fusión en el horno eléctrico, si el baño metálico tenía más carbono del deseado, por ejemplo, si se había usado arrabio o chatarra con mucho contenido en C, se oxigenaba controladamente el baño. Ese oxígeno reaccionaba con el carbono formando monóxido o dióxido de carbono, que se liberaban como gas.
Pero para que esa reacción se produjera de forma eficaz, hacía falta una escoria básica: rica en óxidos como CaO o MgO. Esta escoria no solo facilitaba la oxidación del carbono, sino que además retiraba impurezas como azufre y fósforo, atrapándolas en la fase líquida superior.
Ese proceso no se quedaba ahí. Después venía lo que podríamos llamar una “triple purificación”:
1.- Refinado primario: eliminación de escorias y oxigenación controlada en el horno.
2.- Afino en cuchara: desgasificación y ajuste final de aleantes, muchas veces con gases inertes.
3.- Colada controlada en lingoteras: cuidando el vertido para evitar inclusiones y obtener una estructura interna limpia.
De ahí salían lingotes que se recalentaban y se laminaban en caliente. Esa laminación no era solo para dar forma. También ayudaba a cerrar poros, alinear inclusiones y lo mas importante, refinar el tamaño del grano. Y un grano fino marca la diferencia: aporta tenacidad, homogeneidad y una mejor respuesta al temple.
Cada lote era documentado, tratado térmicamente según su uso y ensayado. Ese nivel de control, desde el horno hasta la herramienta, es lo que daba sentido al símbolo de las Tres bellotas.
El “Calda Tres Bellotas”: el acero para calzar
En un libro que encontré de Aceros Especiales Bellota del 1943 aparece un acero llamado “Calda Tres Bellotas”, descrito como:
“Calidad extra, muy refinado, especial para calda y temple en agua.”
Eso nos dice mucho. Era un acero pensado para ser soldado a la calda sobre hierro blando, o mejor dicho, sobre aceros de muy bajo porcentaje de carbono. Y que al templarlo en agua, respondiera con suficiente dureza sin agrietarse.
¿Cómo se logra eso? Con un carbono medio, muy bajo en impurezas, y sobre todo con grano fino. Porque el grano fino reduce las tensiones internas, distribuye mejor el calor y baja la templabilidad reduciendo grietas. Bellota lo lograba controlando desde la chatarra hasta el laminado final.
Todo apunta a que este “Calda Tres Bellotas” tenía una composición muy parecida al F-114 – F-115 actual (SAE 1045-1050), aunque refinado con más cuidado.
¿Un acero concreto o un estándar de calidad?
¿Las Tres Bellotas identificaban un tipo concreto de acero, una calidad interna del material, o una garantía aplicada al producto final?
La respuesta puede que no sea única.
En el caso del “Calda Tres Bellotas” descrito en el catálogo de 1943, sí parece que existía un acero específico con ese nombre, templable en agua, de grano fino y baja impureza. Muy probablemente un medio carbono (0,55%), refinado y soldable a calda.
Tengo entendido, aunque no he encontrado pruebas, que muchos productos, como hoces, machetes, azadas, el símbolo a veces estaba en el mango, otras en el embalaje. Esto podría reforzar la idea de que el sello se aplicaba con criterio: no todo lo que salía de Bellota lo llevaba. Implicaba ese triple refinado del acero.
¿Por qué era tan respetado?
Era un buen acero, con una fabricación rigurosa y con un excelente control de calidad.
-
Se soldaba muy, muy bien a la calda.
-
Se templaba en agua sin agrietarse.
-
Se conseguía un buen filo.
-
Un acero para herramientas que requieren un trabajo intenso, donde la tenacidad y la dureza requieren un excelente equilibrio.
La soldabilidad a la calda del Tres Bellotas
Una de las razones por las que el acero Tres Bellotas se ganó la confianza de los herreros era su excelente soldabilidad a la calda.
Y esto no era casualidad. Era una cuestión de composición y refinado:
-
El azufre y el fósforo estaba muy controlado, (≈ 0,02 %), lo cual es clave. Estos dos elementos no benefician mucho la soldadura a la calda:
-
El azufre forma sulfuros de hierro (FeS) en los bordes de grano. Estos sulfuros tienen un punto de fusión mucho más bajo que oxido de hierro, se quedan en el límite de grano, y dan fragilidad.
-
¿Por que los herreros antiguos usaban carbón de brezo para soldar a la calda?
EL carbón de brezo, es un carbón vegetal limpio, sin impurezas. Si en el azufre de la hulla.
-
El manganeso, que solía estar alrededor de 0,5–0,6 %, también podría jugar a su favor. El Manganeso es fundamenta, ya que actúa como desoxidante durante la fusión del acero. Además mejora la templabilidad. Un porcentaje moderado ayuda sin perjudicar la soldabilidad.
Además, el acero se fabricaba con triple refinado, lo que eliminaba escorias y dejaba una matriz limpia, homogénea, sin puntos débiles.
Por eso era perfecto para calzar filos sobre cuerpos de hierro dulce.
Y en una fragua es importante y una garantía.
En cuchillería y herramientas:
Se calzaba el “Calda 3 bellotas” para cuchilleria y otras herramientas. Aquí te doy una tabla comparativa de lo que fue este acero, en comparación con el UNE F-1140 o AISI 1045 más moderno.
7. Comparación técnica con F-114
Propiedad | Calda Tres Bellotas (estimado) | F-114 moderno (SAE 1045) |
---|---|---|
% de carbono | 0,45 – 0,55 | 0,35 – 0,45 |
Temple en agua | Sí | Sí |
Soldabilidad a calda | Muy alta | Media |
Pureza estructural | Alta, por refinado | Media-alta |
Reacción al afilado | Grano fino mejora la calidad del filo | Adecuado |
8. Reflexión: el acero que no traiciona
Bellota hoy: ¿siguen produciendo su propio acero?
Sí. Bellota mantiene su acería en Legazpi (también fabrica en otros pasises) con horno eléctrico, control de coladas y tratamientos térmicos. Hoy fabrican aceros para:
-
Herramientas agrícolas, azadas, picos…
-
Cuchillas industriales y recambios.
-
Herramientas forestales y profesionales.
- Herramoentas para la construcción.
Ya no venden su acero como materia prima. Todo lo que funden, lo usan para fabricar sus propias herramientas. Pero el control técnico sigue siendo total: ajustan la composición, afinan el grano y templan con precisión.
Si tú también trabajaste con este acero, si conservas alguna herramienta marcada, o simplemente tienes algo que añadir a esta historia, escríbeme.
Siempre hay más por descubrir cuando hablamos de acero y memoria compartida.